Advancements in Cement Additives for Low-Carbon Emissions
01.07.2025
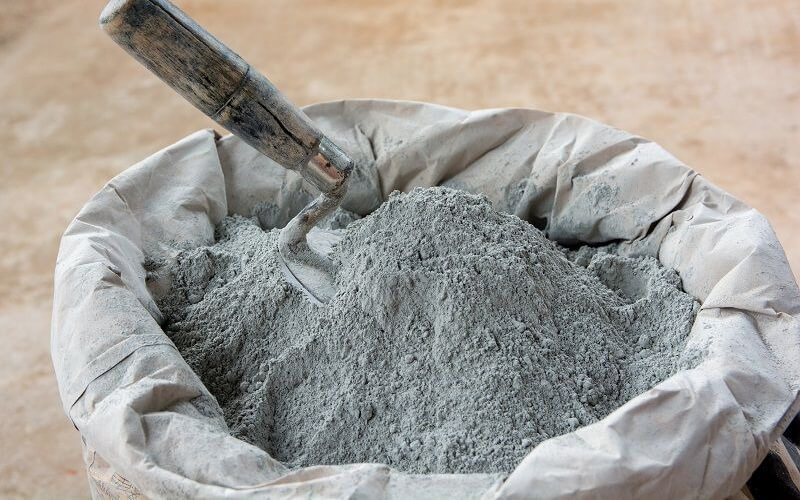
The global construction industry is under immense pressure to reduce its carbon footprint, and cement—one of its most widely used materials—is at the center of this transition. Cement production alone contributes to approximately 7–8% of global CO₂ emissions, primarily due to the energy-intensive process of clinker production. As a response, researchers and manufacturers have turned their attention to cement additives as a key strategy for minimizing emissions without compromising performance.
This article explores the latest advancements in cement additives designed to reduce carbon emissions. From industrial by-products to nano-materials, these innovations are reshaping the future of sustainable cement production and application.
The Role of Additives in Cement Production
Cement additives are substances introduced during the production or mixing stage to modify the properties of cement or concrete. Their primary functions include improving workability, enhancing durability, and accelerating or retarding setting times. In the context of sustainability, additives can also play a vital role in reducing clinker content, increasing the use of industrial waste, and enhancing carbon capture capacity.
By partially replacing clinker or improving hydration efficiency, additives help reduce the overall carbon intensity of cement. This makes them one of the most effective tools for achieving low-carbon construction targets across the globe.
Types of Cement Additives for Emission Reduction
Several categories of cement additives are being developed or refined to reduce CO₂ emissions. These include both traditional supplementary cementitious materials (SCMs) and cutting-edge technological innovations.
1. Fly Ash
Fly ash is a by-product of coal combustion in power plants. It is a well-established SCM that reacts with calcium hydroxide in cement to form additional binding compounds. By replacing a portion of the clinker, fly ash not only reduces emissions but also enhances long-term strength and durability.
2. Ground Granulated Blast Furnace Slag (GGBS)
GGBS is derived from the steel manufacturing process. It is used to replace clinker content in cement, lowering emissions and improving resistance to sulfate attack, chloride ingress, and high temperatures. Its slow hydration rate also improves the workability of concrete in hot climates.
3. Silica Fume
Produced as a by-product of silicon and ferrosilicon alloy manufacturing, silica fume contains extremely fine particles of amorphous silica. It improves the microstructure of concrete, increases strength, and reduces permeability. Its high pozzolanic reactivity contributes to better cement performance with less environmental cost.
4. Calcined Clay (LC3 Technology)
Limestone Calcined Clay Cement (LC3) uses a combination of calcined clay and limestone to replace large amounts of clinker. This method can reduce emissions by up to 40% while maintaining similar strength and durability. The widespread availability of clay makes LC3 a promising solution for emerging markets.
5. Natural Pozzolans
Volcanic ash, pumice, and other naturally occurring pozzolans have been used since ancient times. These materials are increasingly being researched for modern applications due to their ability to reduce clinker content and improve chemical resistance. They are especially valuable in regions with easy access to natural deposits.
6. Carbon Capture Additives
Some new additives are designed to actively capture and mineralize CO₂ within the concrete matrix. These include reactive magnesium oxides and nano-calcium carbonate, which sequester carbon during curing. Such innovations turn concrete into a potential carbon sink rather than a source.
7. Nano-Additives
Nano-silica, nano-alumina, and graphene oxide are among the emerging nano-additives that enhance cement hydration and strength. These materials allow for lower cement dosages without compromising performance, indirectly reducing CO₂ emissions associated with production.
Performance Benefits of Low-Carbon Cement Additives
In addition to reducing emissions, many cement additives offer performance improvements that contribute to the sustainability and longevity of structures:
- Increased durability: Additives improve resistance to chemical attacks, temperature changes, and environmental degradation.
- Enhanced strength: Certain pozzolanic materials and nano-additives increase both early and long-term compressive strength.
- Improved workability: Additives help maintain fluidity and consistency in concrete, even with lower water-to-cement ratios.
- Shrinkage control: Additives reduce shrinkage and cracking, improving the structural integrity of buildings.
- Thermal performance: Some additives enhance insulation properties, lowering the energy demand of buildings.
These benefits extend the lifespan of concrete structures, reducing the need for repairs and rebuilds, which also contributes to lower lifecycle emissions.
Challenges and Limitations
Despite the promise of cement additives in reducing emissions, there are several challenges to widespread adoption:
- Availability: Industrial by-products like fly ash and slag are dependent on other industries and may decline with cleaner energy transitions.
- Standardization: Building codes and regulations in many regions still favor traditional cement mixes, slowing the approval of additive-based formulations.
- Cost: Some advanced additives, especially nano-materials, are still expensive and not viable for large-scale use without subsidies or technological breakthroughs.
- Performance consistency: Variability in additive quality, especially from waste sources, can affect performance and reliability.
Addressing these challenges will require cross-industry collaboration, policy support, and continued research into scalable, cost-effective additive technologies.
Recent Innovations in Cement Additive Technology
Ongoing R&D efforts have led to the emergence of several innovative solutions in the cement additive space:
- Bio-based additives: Researchers are exploring algae-derived silica and cellulose-based additives for carbon-neutral formulations.
- Hybrid systems: Combinations of traditional SCMs with nano-additives are being tested for synergistic performance gains.
- Self-healing concrete: Additives with microencapsulated healing agents repair cracks autonomously, extending service life and reducing material consumption.
- Digital mix design: AI-driven platforms are optimizing mix ratios to achieve desired performance with the lowest possible emissions.
These innovations show how the cement industry is moving toward smart, green, and high-performance building materials for the future.
Global Impact and Policy Alignment
The development and adoption of low-carbon cement additives align closely with international climate goals. Organizations such as the Global Cement and Concrete Association (GCCA), the International Energy Agency (IEA), and national governments have highlighted the role of SCMs and additives in achieving net-zero emissions by 2050.
Policies such as carbon pricing, green procurement, and building certification programs (e.g., LEED, BREEAM) provide incentives for adopting additive-enhanced, low-carbon cement. These frameworks are critical in driving innovation and scaling up adoption across the industry.
Conclusion
Cement additives represent a practical and effective pathway toward reducing the carbon intensity of one of the world’s most essential construction materials. Through the use of industrial by-products, natural pozzolans, and advanced nano-technologies, cement manufacturers can achieve substantial emission reductions without sacrificing performance or affordability.
As research progresses and regulatory frameworks evolve, the widespread adoption of low-carbon cement additives will play a pivotal role in meeting the sustainability goals of the construction sector. The future of cement is not just stronger and more durable—it is smarter, cleaner, and more environmentally responsible.