How Cement is Made: The Complete Manufacturing Process
06.03.2025
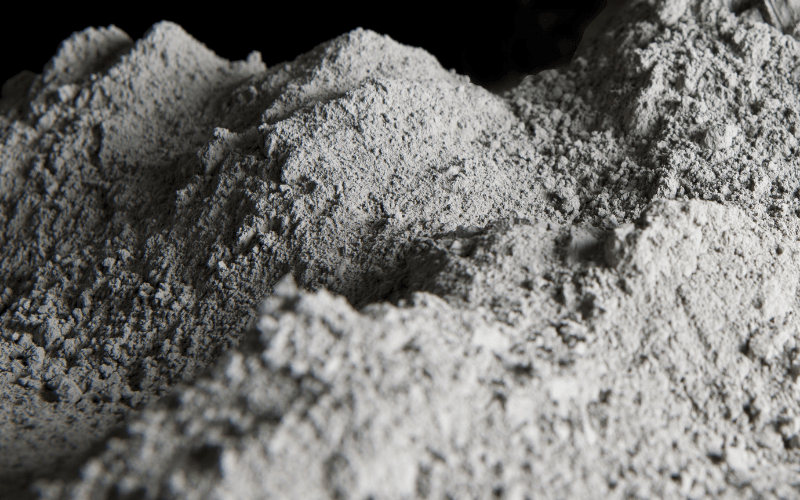
Introduction
Cement is a crucial building material used in construction projects worldwide. The manufacturing process involves a series of steps that transform raw materials into a strong and durable binder for concrete. Understanding how cement is made helps in optimizing production efficiency and ensuring high-quality output.
Raw Materials Used in Cement Production
- Limestone: The primary ingredient, providing calcium carbonate (CaCO₃).
- Clay: Supplies silica, alumina, and iron oxide, essential for the chemical composition.
- Sand and Shale: Additional sources of silica that enhance strength.
- Iron Ore: Helps adjust the mix's chemical balance.
- Gypsum: Regulates the setting time of cement.
The Cement Manufacturing Process
1. Mining and Extraction
The process begins with the extraction of limestone, clay, and other raw materials from quarries or mines. These materials are then transported to the cement plant for further processing.
2. Crushing and Pre-homogenization
Large rocks are crushed into smaller pieces using jaw crushers and hammer mills. The crushed materials are mixed in specific proportions to ensure a uniform composition.
3. Raw Material Grinding
The crushed materials are ground into fine powder in a ball mill or vertical roller mill. This fine powder, known as raw meal, is then stored in silos for further blending.
4. Preheating and Calcination
The raw meal is fed into a preheater tower, where it undergoes a series of heat exchanges. It then enters a rotary kiln, where calcination takes place at temperatures around 1450°C, forming clinker.
5. Clinker Cooling
The hot clinker is rapidly cooled using air or water to stabilize its properties and prepare it for grinding.
6. Cement Grinding
The cooled clinker is mixed with gypsum and ground into a fine powder in a cement mill. The final product is known as Portland cement, which is stored in silos.
7. Packaging and Distribution
Cement is packed in bags or transported in bulk to construction sites and suppliers. It is then ready for use in concrete production and other construction applications.
Environmental Considerations in Cement Manufacturing
- Energy Efficiency: Using alternative fuels and renewable energy sources reduces carbon emissions.
- Emission Control: Advanced filtration systems help minimize dust and gas emissions.
- Waste Utilization: Fly ash, slag, and other industrial byproducts are used to reduce raw material consumption.
- Water Conservation: Recycling and efficient water management practices reduce wastage.
Conclusion
The cement manufacturing process is a complex yet essential operation in the construction industry. From raw material extraction to the final product, each step plays a vital role in ensuring cement quality and sustainability. With technological advancements, cement production continues to evolve, focusing on efficiency and environmental responsibility.